-
Details
-
Written by Cynthia Chuah
-
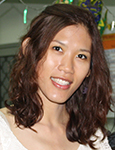
Guidelines for evaluating the DAC for your needs.
Read more ...
-
Details
-
Written by Mike Buetow
-
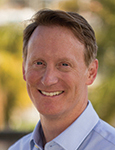
Catching up on your summer reading? Consider Dickie: Memoirs of a Mad Scientist, by Richard Nedbal.
Read more ...
-
Details
-
Written by Peter Bigelow
-
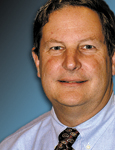
The misperceptions outsiders hold of the PCB industry are damaging to people and profits.
Read more ...
-
Details
-
Written by Susan Mucha
-
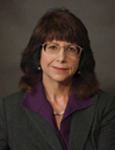
A consistent, frequent message will ensure you aren’t the industry’s best-kept secret.
Read more ...