-
Details
-
Written by Robert Boguski
-
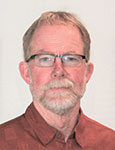
Test engineering, done correctly, is a bearer of bad news. Who wants that?
Read more ...
-
Details
-
Written by Rajesh Upadhyaya
-
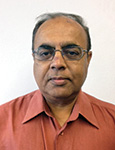
Root cause identification and corrective action brought higher yields for an automotive PCB.
Read more ...
-
Details
-
Written by Dr. Chris Hunt
-
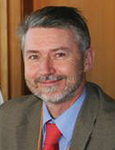
Exhausted flux can cause incomplete reflow.
Read more ...
-
Details
-
Written by Joseph Fama
-
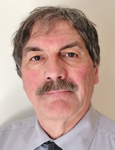
China’s labor problems put India’s EMS capability in a new light.
Read more ...